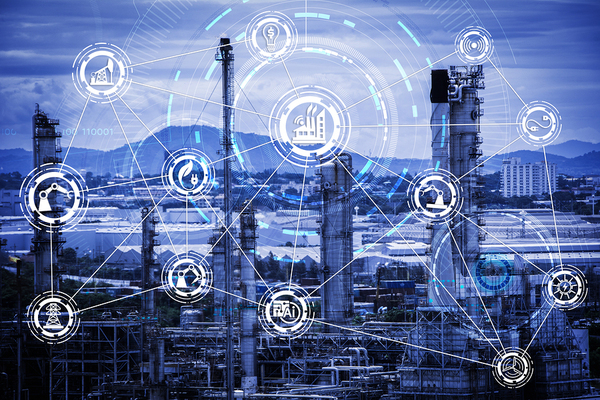
The smart factory is revolutionizing how things are made today, propelled by a convergence of technologies that are transforming operations and providing safer, more efficient, and more dynamic workplaces.
As seen in the recent post, Digital Transformation: Is Your Organization Ready, technologies are changing how industries function, requiring new tools to integrate work teams, processes, data, and decision-making. It means companies need to think deeply about how to maximize the impact of these changes and prepare for inevitable new disruptive technologies to come. Here is a look at some of the technologies changing manufacturing in the digital age.
Defining the Smart Factory
The smart factory today is one that expands on several technologies and introduces new ones. At its core, the smart factory expands the use and impact of automation, allowing for new applications beyond the robotic completion of simple, repetitive tasks.
Today, automation uses artificial intelligence, the Internet of Things, and virtual reality to connect physical objects like never before. The connected objects, tools, and machines in a smart factory collect, store, transmit, and use information generated from processes.
This information can be used to optimize production, pinpoint needed maintenance or repairs, diagnose inefficiencies, and complete tasks. Machines can learn based on past performance and identify opportunities to improve performance.
Smart factories generate massive amounts of data from the connected objects within. Cloud-based platforms can collect this data, store it, and present it in cogent ways that help workers make better decisions.
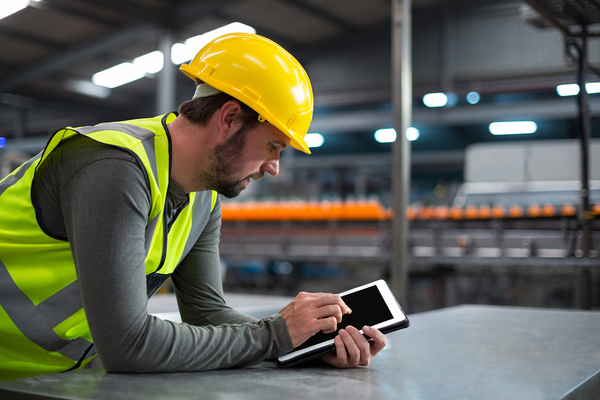
Five Features of a Connected Factory
The connected factory today is highlighted by several key factors.
Connected. The smart factory continues to pull traditional data sets and new data generated from connected objects. The data together provide insights on accuracy, usage, performance, and temperature, all of which help lead to better decisions.
Optimized. The smart factory uses collected information to reduce waste and maximize performance. The need for manual work is reduced as automated processes can be used to optimize workflows, scheduling, energy consumption, asset integration, and tracking.
Transparent. Data from across the factory enterprise allows for the transparent display and use of information in real time. Transparency can extend throughout the supply chain, leveraging shared insights for better use of materials, logistics, transportation, and warehouse management. With transparent data shared internally, changes to policies and procedures can be identified and deployed more quickly.
Proactive. Predictive analytics help improve many areas of the smart factory. Anomalies can be detected faster, reducing down time for necessary maintenance and repairs. Anomaly detection also helps maintain better inventory insights, and react to delivery delays or lack of availability of materials. Safety improves, both for operations and in the quality of products.
Agile. Optimizing production capacity is important and can leverage the data and analytics tools to create recommended production schedules, minimize downtime, and accelerate changeovers.
The Tools Needed
The smart, connected factory leverages data from multiple areas, both on the factory floor and in back-office functions such as accounting, finance, and HR. An enterprise resource planning (ERP) platform brings these data and technologies together in powerful ways.
At Denovo, we help clients create smarter, more connected environments with cloud ERP solutions. Our expertise in creating scalable platforms that grow as an organization’s needs evolve helps companies get the most out of the innovative technologies transforming work. To learn more about how Denovo can help your company leverage the digital revolution, schedule a free consultation.
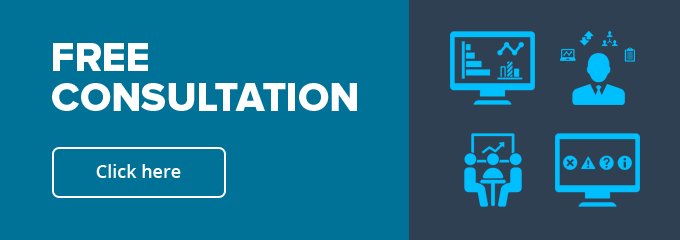
Share this look at how smart factories provide more transparency, efficiency, and connectivity throughout the manufacturing enterprise @DenovoCloud #CloudERP #SmartFactory.